Viral Vectors: collaboration is key to fixing stability and other challenges
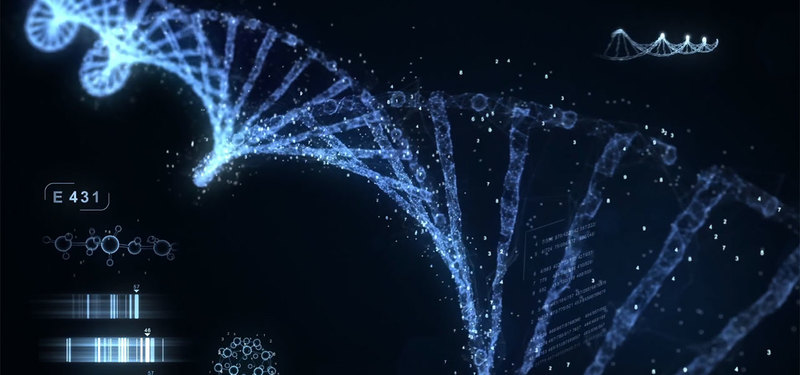
As cell and gene therapies continue to develop and get approved as treatments, standardized, safe workflows for viral vector production are critical.
Viral vectors are created using part of the structure of a specific virus and are effective because of the natural ability of a virus to enter a cell.
Because the vector is the delivery mechanism for the therapy, the vector manufacturing process must be optimal for the end therapy to be effective.
Problems that occur with some current methods include:
- Vectors can cross-link and form aggregates that can cause the vectors to lose therapeutic efficacy and lead to unwanted immune response. Aggregates can also increase the viscosity of the vector solution, making it difficult to load the vector into syringes.
- Loss of vector stability, so the therapeutic load will not reach targeted cells.
- Environmental issues— vectors can oxidize upon exposure to light or due to metal ion impurities in the raw materials used in manufacturing. Temperature fluctuation can destabilize vectors.
- The pH and ionic strength of vector formulations can also impact vector stability and infectivity.
While there are known solutions, this expanding field requires deliberate attention around processes. If one biopharma manufacturer knows to use a different excipient like high purity sugar, to help with stabilization, and another knows that refrigeration can help with both aggregation and loss of effective infectivity, sharing this knowledge will speed the process of getting life changing treatments to patients globally.
Arvind Srivastava, Technical Fellow, shares his insights into challenges in viral vector production and makes the case for drug manufacturers and chemical and excipient suppliers to work together to standardize the process in an opinion piece published in The Medicine Maker.
Read more about his approach to problem solving
Author
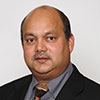
Arvind Srivastava, Ph.D.
Technical Fellow, Research - Bioprocessing
Dr. Arvind Srivastava is a Vice President at Avantor, leading contract development and manufacturing organization (CDMO). Before joining Avantor, Dr. Srivastava was Research Advisor at Eli Lilly and Company, where he managed drug product development from early development stage through commercial registration. Dr. Srivastava did his postdoctoral training from the University of North Carolina at Chapel Hill, NC, USA. He got his Ph.D. degree in biochemistry from the prestigious Tata Institute of Fundamental Research (TIFR) and M.S. in chemistry from the Banaras Hindu University (BHU). Dr. Srivastava has published numerous papers in international journals and has been frequently invited to present his research at the national and international conferences.
Customer support
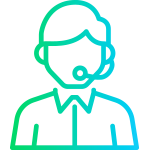
Contact us
Ready to streamline your bioprocessing manufacturing workflows? Avantor Biopharma Production can help.