Removing bottlenecks in downstream processing purification
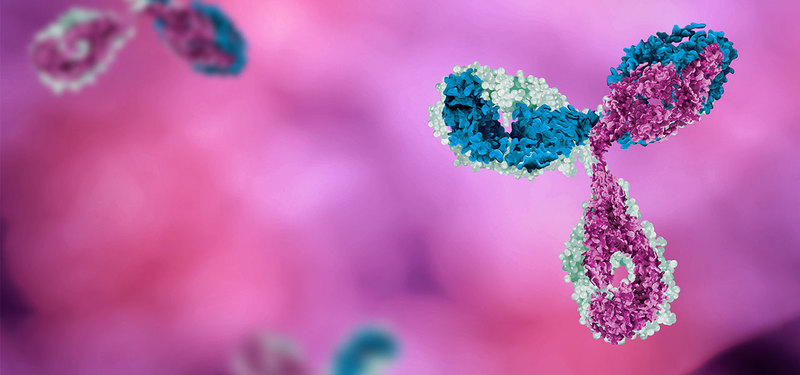
In the production of monoclonal antibodies (mAbs), finding ways to remove bottlenecks and improve yields in downstream processing continues to be a key focus area for biopharma manufacturers. Downstream processing generally takes place over a period of a few weeks and involves many unit operations – from multiple chromatographic steps and filtration steps, and more than a dozen buffers and cleaning solutions as part of the process. In fact, about 60-80 percent of the total cost of producing a mAb can be attributed back to downstream processing[1].
A capture step is the first purification step where protein A has become the most widely used resin due to its highly specific nature, ease of implementation as a standard purification process, and strong regulatory track record[2] . It is well known that the cost of the protein A capture step is substantial, and that buffer preparation is an area for improvement to help improve both cost and efficiency.
In this article, we will highlight strategies to improve the productivity of the capture step through the selection of a high performance protein A resin and optimization of buffer preparation. Buffer preparation will be further discussed by comparing in-house buffer preparation and ready-to-use buffers, or buffer concentrates utilizing latest technologies and supply chain options.
Authors
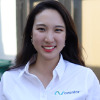
Dr. Jungmin Oh
Manager, New Product Development
In her current role, Jungmin leads product and process development projects with multiple biopharmaceutical industry partners, including customized product development for cell and gene therapy customers. She holds a MS and Ph.D. in chemical engineering, specializing in the optimization of a continuous chromatography system.

Dr. Pranav Vengsarkar
Manager, Research & Development – Biopharma Production
Pranav Vengsarkar, Ph.D., is Manager, Process Development at Avantor, focused on product and process development for new cGMP products and excipients, and development and design of single-use raw material delivery systems. Pranav holds a Bachelor of Chemical Engineering degree from ICT, Mumbai and a Ph.D. in Chemical Engineering from Auburn University.
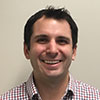
Dr. Jonathan Fura
Manager, Research & Development
In his current role, Jonathan focuses on developing technologies that are utilized to advance the development and manufacturing of antibody-based biopharmaceuticals and diagnostics. Jonathan holds a Ph.D. in chemistry with a focus on developing immunomodulation therapeutic strategies.

Dr. Nandu Deorkar
Ph.D., MBA, Senior Vice President, Research & Development – Biopharma Production, Avantor
Nandu Deorkar is Senior Vice President, Biopharma Production Research & Development for Avantor. He is responsible for innovation strategy and planning, and execution of new products and technology development. During his more than 25-year career in research & development, Dr. Deorkar has been leading teams working on various aspects of upstream and downstream bioprocessing, single use systems, chemical/polymer R&D, drug development, formulation, drug delivery technologies, process development, and technology transfer. He has published more than 30 articles and holds more than 20 patents. Dr. Deorkar received Ph.D. from Indian Institute of Technology, Mumbai, India and MBA in Marketing from Fairleigh Dickinson University, Madison, NJ, USA.

Solutions for bioprocessing
From the small-scale bench to full commercial manufacturing, we enable our customers to reach the market with new treatments for patients, faster and safer. Learn more about our offering for biopharmaceutical manufacturing.
Customer support
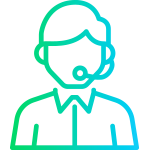
Contact us
Ready to streamline your bioprocessing manufacturing workflows? Avantor Biopharma Production can help.