Industry perspective: much needed advances in biopharma chromatography

The objective of downstream chromatography in mAbs therapeutics manufacturing is simple – remove any process-related contaminants that occurred upstream and remove any product-related impurities. But the full manufacturing process aimed to meet that objective is complex, often involving multiple chromatographic and filtration steps.
Yet, the market for mAbs treatments is one of the fastest growing biopharma markets. This means biopharma manufacturers need to improve their processes as they develop and scale up production.
In Pharma Manufacturing, Dr. Nandu Deorkar, Avantor’s Vice President of Research and Development explains the purpose of chromatography in downstream processes of mAbs therapeutic manufacturing. He also describes the challenges of manufacturing a safe and effective final product – and the role of Avantor’s premium protein A chromatographic resin and single-use technologies to address these challenges.
The downstream operation has necessary auxiliary steps to make sure product being loaded into the column has specific buffer composition, pH and conductivity. But each step further complicates and can slow down manufacturing. A two or three step chromatographic system has three chromatography steps, and each of those steps can require up to four auxiliary steps.
Downstream purification of mAbs often uses a protein A chromatographic resin for affinity chromatography. Because this method of purification is so effective, typically only one or two standardized polishing steps are then required.
Increasing the volume of material purified, by using an excellent protein A like J.T.Baker® BAKERBOND® PROchievA™ which increases the dynamic binding capacity of the material, means fewer cycles and increased productivity.
So, resin choice can have a positive effect even when using current equipment. By increasing the dynamic binding capacity of the resin, operators can accomplish more with the same equipment.
Single-use technologies and equipment, however, offer more options to improve. A single-use system for buffer preparation and media preparation eliminates time-consuming and costly cleaning steps, which adds to the overall efficiency of the process.
In most circumstances using a platform approach, that is, a specific set of equipment or a specific process for biopharma manufacturing, is usually best practice.
Learn more about Dr. Deorkar’s insights
Author

Dr. Nandu Deorkar
Ph.D., MBA, Senior Vice President, Research & Development – Biopharma Production, Avantor
Nandu Deorkar is Senior Vice President, Biopharma Production Research & Development for Avantor. He is responsible for innovation strategy and planning, and execution of new products and technology development. During his more than 25-year career in research & development, Dr. Deorkar has been leading teams working on various aspects of upstream and downstream bioprocessing, single use systems, chemical/polymer R&D, drug development, formulation, drug delivery technologies, process development, and technology transfer. He has published more than 30 articles and holds more than 20 patents. Dr. Deorkar received Ph.D. from Indian Institute of Technology, Mumbai, India and MBA in Marketing from Fairleigh Dickinson University, Madison, NJ, USA.
Customer support
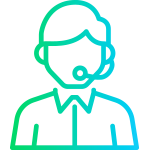
Contact us
Ready to streamline your bioprocessing manufacturing workflows? Avantor Biopharma Production can help.