Improving mAb Manufacturing Productivity by Optimizing Buffer and Media Prep Process Flow
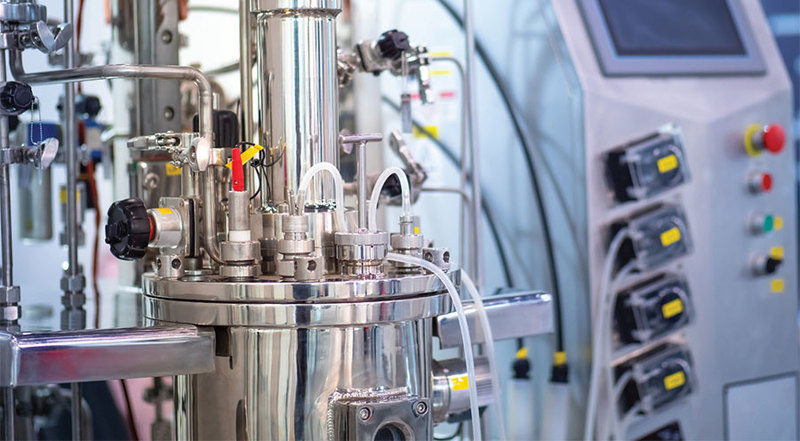
It is common for biologics manufacturing processes to require hundreds of raw materials, ranging from media and media supplements, buffers, and salts to other process chemicals. Buffers and salts are typically the largest constituents by volume used in the downstream processing steps for manufacturing most biopharmaceutical products. A typical monoclonal antibody (mAbs) (mAb) process may require 2000 L of a buffer and more than 100,000 L per batch based on titer and bioreactor volume (1, 2). As a result, the variety of buffer solutions used across a biopharma manufacturing facility requires flexible, cost-efficient infrastructure and on-time delivery to meet process demand.
At the same time, the growing use of single-use systems offers many advantages in managing raw materials used in bioprocessing. Single-use technologies add flexibility, reduce capital requirements, and improve ease-of-use in biopharma manufacturing operations. Solid or hydrated buffers and salts that come ready-to-dispense in single-use bags and buffer preparation using single-use systems, reactors, and in-line dilution can both help eliminate or reduce weigh and dispense operations.
The modularity of single-use systems allows site-specific and process-specific solutions to be implemented quickly without requiring significant capital expenditure. Single-use raw material delivery systems, in powder or liquid form, can help reduce the risk of contamination and minimize the need for frequent cleaning steps. Raw material quality control (QC) testing can also be reduced or eliminated by implementing single-use technologies, saving time from reduced process steps as well as labor costs.
The increase in titers and the trend toward continuous biomanufacturing will lead to increased demand in buffer volumes and prep times. To address this gap, strategies for improving mAb manufacturing productivity by optimizing powder and liquid buffer and media prep process flow are worth considering. When combined with innovative new technologies such as in-line dilution, single-use powder and liquid formulations can help reduce facility footprint, labor hours, and the overall cost of goods.
Authors

Dr. Nandu Deorkar
Ph.D., MBA, Senior Vice President, Research & Development – Biopharma Production, Avantor
Nandu Deorkar is Senior Vice President, Biopharma Production Research & Development for Avantor. He is responsible for innovation strategy and planning, and execution of new products and technology development. During his more than 25-year career in research & development, Dr. Deorkar has been leading teams working on various aspects of upstream and downstream bioprocessing, single use systems, chemical/polymer R&D, drug development, formulation, drug delivery technologies, process development, and technology transfer. He has published more than 30 articles and holds more than 20 patents. Dr. Deorkar received Ph.D. from Indian Institute of Technology, Mumbai, India and MBA in Marketing from Fairleigh Dickinson University, Madison, NJ, USA.

Dr. Pranav Vengsarkar
Manager, Research & Development – Biopharma Production
Pranav Vengsarkar, Ph.D., is Manager, Process Development at Avantor, focused on product and process development for new cGMP products and excipients, and development and design of single-use raw material delivery systems. Pranav holds a Bachelor of Chemical Engineering degree from ICT, Mumbai and a Ph.D. in Chemical Engineering from Auburn University.

Solutions for bioprocessing
From the small-scale bench to full commercial manufacturing, we enable our customers to reach the market with new treatments for patients, faster and safer. Learn more about our offering for biopharmaceutical manufacturing.
Customer support
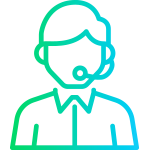
Contact us
Ready to streamline your bioprocessing manufacturing workflows? Avantor Biopharma Production can help.